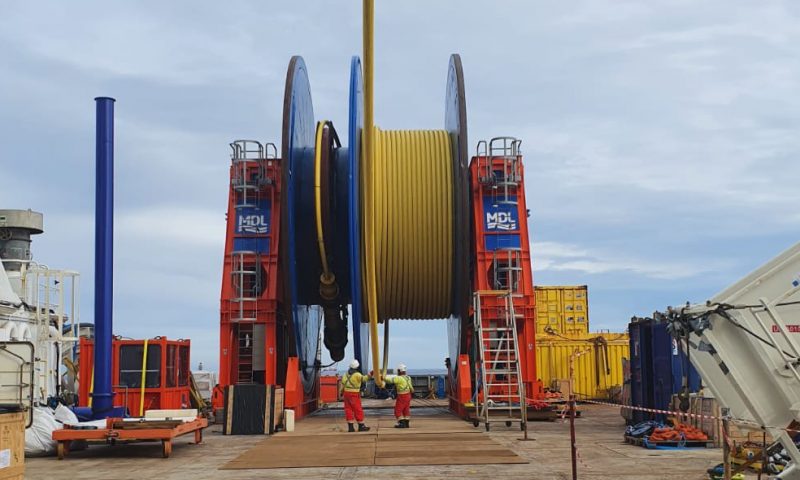
Tailored Tie-Back Sees RDS Reel Capacity Increased
MDL has completed a North Sea tie-back, which included delivery of a bespoke solution for handling reels of 12m diameter.
The work scope covered installation of 3 reels of flowlines, jumpers and an umbilical using MDL Third-generation Reel Drive System. The reels measured from 9.2m to 12m diameter – the largest reel handled by the MDL RDS to date.
To accommodate the larger diameter, MDL designed and manufactured in-house a bespoke set of 12m cradles to safely integrate with the MDL Track and Cradle System, optimising mobilisation and demobilisation times.
As standard, the MDL RDS track system comes complete with integrated cradles, supplied with boltable inserts to accommodate varying diameter reels, resulting in a saving on mobilisation time by eliminating sea fastening of the reels and cradles.
The system’s lashing points are designed for fastening the reels to the tracks instead of welding multiple fixing points to the vessel deck, which also saves time and engineering costs.
A further time efficiency comes from the RDS design, where the HPU is built into one of the towers, reducing the space taken up by the system on deck and the associated sea-fastening design and execution requirements.
The MDL Third-generation Reel Drive System was also a benefit to the client as the towers can engage with the smallest 9.2m reel and stroke to the largest 12m reel without the need for any packers or interim mobilisation.
On this project the RDS had already been mobilised on the vessel, as the tie-back was a follow-up scope in a multi-project campaign – further adding to MDL efficiencies.
Dave Gardiner, MDL VP UK & Europe, said: “We take up a partnership approach with every client, where we jointly discuss their upcoming campaigns and identify possible time and cost efficiencies. That was the case on this project – part of a larger campaign with the client using the same vessel.
“By keeping the RDS and track system on board in between projects, we reduced the design and engineering workloads pre-mission and optimised the mobilisation times for the equipment and product across the campaign to date.
“MDL was also the most cost-effective option to deliver the cradles for the client’s 12m reel. We combined our 20-year track record in equipment design and manufacture with the in-house data on our track system, to safely and efficiently integrate the new cradles with the spread already on board the vessel.
“As we hope to continue the successful relationship with this client – now in its seventh year of working together globally – we are always on a lookout to further add value to their operations.”