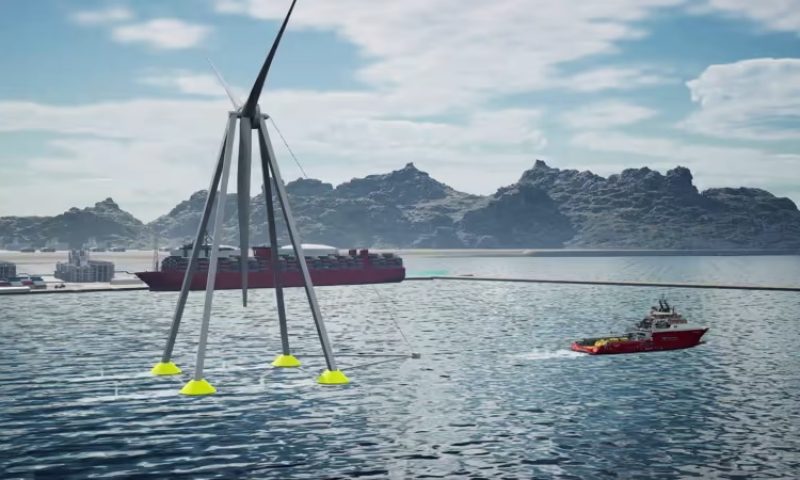
T-Omega re-thinks floating offshore wind turbines for huge cost savings
Most of the world’s greatest wind power resources are offshore – often a long way offshore, where the water’s so deep that it’s impractical to build typical fan-on-a-stick wind turbines with bases sunk deep into the sea floor. Floating wind, at this stage, is so vastly expensive to build, deploy and maintain that it ends up costing two to three times as much per kilowatt-hour of energy as fixed-bottom offshore installations.
There’s a huge opportunity here for technological advancement, and companies like Norway’s World Wide Wind are proposing some pretty radical ideas in the space. A lot of the energy cost comes down to the size, weight and materials involved in the structure of the turbine, along with the logistical issues and specialized equipment needed to build, install and maintain the things.
Boston startup T-Omega Wind says it’s model-tested a unique floating offshore wind turbine design that can withstand massive storms and hundred-foot waves, but at 20% the weight and around 30% the price of conventional designs – not to mention super-simple deployment and installation – unlocking an affordable way to exploit the world’s best wind resources.
“All offshore floating turbines except ours are like icebergs,” says T-Omega Co-Founder and Chief Engineer Jim Papadopoulos over a video chat. “Whatever they’ve got above the water, they’ve got four times as much below the water. If they’ve got 1,500 tons above the water, they’ve got 6,000 tons under the water. That’s a big expense. We put almost nothing under the water. That’s one of the big differences in cost, and movability, and launching.”
Conventional floating turbines, says Papadopoulos, use technology that was only ever designed for land. “Right now, a Vestas or GE-style turbine, they have a whacking great rotor, with a shaft on one side. You can engineer almost anything, but with a single-sided shaft, that shaft is massive, and requires some pretty special bearings. And because of the forces that go through that design, there’s very little strength margin to shake it around. So they have to hold them dead still, perfectly upright – hence, the heavy, expensive base. They’re imbued with a land-style philosophy, and it’s incredibly expensive.”
T-Omega’s approach is completely different, starting at the turbine and generator itself, which mount to a double-sided axle shaft that’s rigidly supported at both ends. Thus, rather than a single, heavyweight pole, the turbine is supported by four much slimmer legs, reaching down to lightweight, wide-spaced floating base platforms. It’s much like the way a Ferris wheel is suspended; there’s a reason why they don’t usually build those on a single pole.
T Omega Wind Turbine Full 3D Video
Will it capsize?
“If you took a wooden door and put it in the water, it’s not going to tip over,” says Papadopoulos. “It’s the width compared to the height. So yeah, we have a very wide base compared to any other floating design. To lift the floats out of the water, you’re looking at an ungodly amount of torque – it’s much more than the generator torque.”
The floating base is tethered to the sea floor, and as the wind changes, the base rotates freely around its pivot point on the sea bed, such that it’s always facing directly into the wind – but without needing any sensors, motors and pivoting mechanisms to achieve that end. The tower of such a system can be wide and efficient for enormous cost savings, says Papadopoulos.
“Suddenly, the weight of the tower can be something like 15-20% of the weight of a normal tower. And instead of dealing with two- or three-inch thick steel – and all the equipment and time and logistics that entails – you’re dealing with half-inch steel or less, and anybody can cut and weld it.”
This follows through to the gear up top, as well. Supported by both ends, the T-Omega design doesn’t need the same kind of massive hub and axle designs conventional turbines need, simply to deal with the enormous stress imposed by a single-sided axle. That means less metal, less weight, less specialized tooling, and less cost at every step of the way. It also means a wider range of fabrication businesses can build the things.
The company built a two-meter-high (6.5-ft) prototype – a 1:60 scale model of a commercially-sized 10-MW product, and tested it for stability in a wave tank in Glasgow.
“This is the lightest 1 to 60th scaled floating wind model I have ever tested,” said Dr. Saishuai Dai, project manager of the Kelvin Hydrodynamics Laboratory, in a press release. “The model successfully rode a storm sea state with an equivalent full-scale significant wave height of 18 meters (59 ft). A 30-meter (98-ft) full-scale equivalent maximum wave height was observed within that storm sea state, and it was pushing the upper limit of our wavemakers.”
“Those waves are the equivalent of 100 feet high,” says Papadopoulos. “This thing was rocking like a fairground ride. No problem.”
T-Omega Wind Strathclyde Tank Test
Since the design doesn’t extend down very far under the water, deployment is far simpler. You can put these things together at a dock – or even without one, float them straight into the water, and then tow them out to site. Maintenance is much the same; unhook the turbine, tow it back to shore, do whatever maintenance is required, then swap it back into the live wind farm rotation when you’re done. No need for jack-up ships or floating cranes, you simply tow the turbines back in to port where everything’s easy.
“We’re aiming for the lowest possible cost,” says Papadopoulos. “And part of our play is to say, we’re not going to aim for 25 years without maintenance. We’ll replace parts in a few years if they’re cracking, because we’ve made that easy. Conventional turbines are insanely expensive to maintain – you’ve got to rent a heavy crane ship for two or three million pounds a week, and even then it’s only possible in brilliant weather. They wait until two or three have failed to justify the cost of that ship – and to avoid that, they build them to last forever. That’s one of the reasons they’re so expensive. They want perfection in their design. We don’t. The costs work out much better.”
Where nearly every other offshore wind design is looking to endlessly scale up with bigger and bigger turbines, T-Omega says its economical sweet spot will be about half the size of today’s biggest turbines. “Everyone else seems to love the idea of getting bigger,” says Papadopoulos, “but we hate the idea of massive size, because it means you need bigger ports, bigger ships, bigger everything.”
And, he says, T-Omega’s proposition is fundamentally different.
“Why are they getting so big?” he asks. “What’s happening is that it installation and maintenance costs are so insane for these turbines, that you’d rather install and maintain one giant one than two medium ones. But those costs don’t apply to us. And there’s something called the square-cube law; when you double the size of a turbine design, you increase the swept area of the rotor by four times – but the weight goes up eight times, because you’re doubling the height, width and length of every part in three dimensions. So it’s actually a losing proposition to go too big for us. We’re probably going to find our sweet spot with the lowest electricity cost at somewhere around 7-8 megawatts.”
Supporting the turbine at both ends means T-Omega can get away with much simpler, cheaper, lighter generators and support structures
Supporting the turbine at both ends means T-Omega can get away with much simpler, cheaper, lighter generators and support structuresT-Omega Wind
The company projects a Levelized Cost of Energy (LCoE) around US$50 per megawatt-hour in internal calculations. It’s working to have this figure re-run by an independent third party.
“According to our numbers,” says Papadopoulos, “we’re in the ballpark of the best fixed-bottom offshore wind available today.”
At this point, T-Omega is a small group of people, financing prototypes through grant money and accelerator funds.
“We’re just starting to seriously look for investment,” says Papadopoulos, “We think that this is this could be the most versatile, easy to build, cheapest floating wind turbine that’s being proposed. So why wouldn’t everybody want it? Maybe that’s naive!”
Indeed, there are some other massive market forces in the way.
“We explained our concept to an ex-CEO of a company making some of the biggest turbines in the world,” says Papadopoulos, “a guy who really knows the business. We showed him our design. He said admiringly, ‘that’s a really great design. Everybody needs it. It’ll make the maintenance easier. It will make building and installing it easier. It’s a great thing. I give you zero chance of success.’ And we looked at him all crestfallen and asked why. And he said, ‘well because just before I left, we just invested three or four billion in making things the old way. Do you think we want to throw away that factory?’ So the big turbine makers aren’t very interested, they apparently want to keep selling what they make now.”
So the challenge for T-Omega is to find manufacturers that aren’t locked into legacy technology. Papadopoulos says the company has a few lines in the water with investors, but that it’s yet to land a deal that could finance the next step: a 100-foot-high design that could end up being a product for smaller coastal settlements and islands.
Floating offshore wind turbines will play a critical part in the clean energy transition – but their contribution will be limited by their cost. It’s a sector ripe for technological disruption, and T-Omega’s refreshingly simple approach seems to have a lot to offer. We wish the team well in pushing the project forward, and look forward to hearing how it progresses.
Check out an animation giving further detail on the process of building, installing and maintaining T-Omega’s turbine design in the video below.
TOW_001_ExplainerAnimations_v0.6_SB