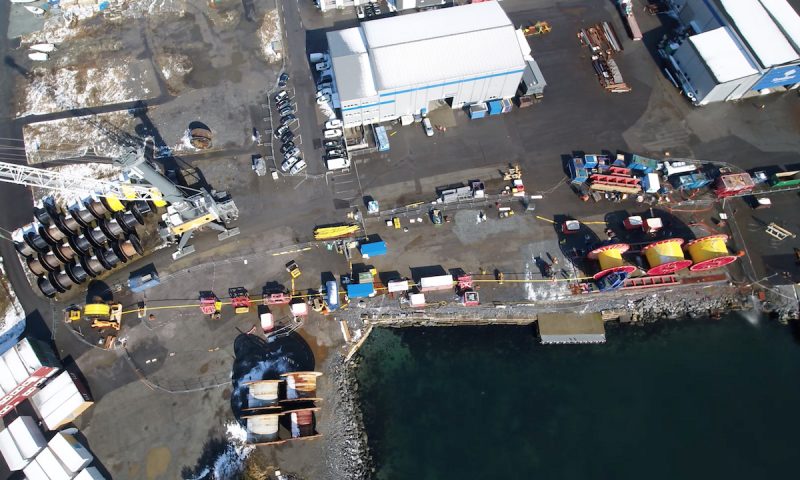
MDL Completes Double Transpooling in Norway
MDL has carried out transpooling of 64km of MEG coiled tubing for two subsea contractors: Ocean Installer and DeepOcean, kick-starting cost efficiencies ahead of their respective offshore missions.
The operation consisted of transpooling MEG injection lines from 28 Tenaris transportation reels onto 7 Client-supplied offshore installation reels for two separate subsea installation projects, using MDL flex-lay spread operated by the company’s expert technicians.
MDL project managed and engineered the complete operation, which included: project engineering, scheduling, transpooling procedures, task plans, mob/demob procedures, straightener testing, reeling verifications, back tension for spooling calculations, straightening analysis, general equipment list, data sheets and general arrangements, transpooling equipment setup/layout, lift plans, HAZID/HAZOP and marine personnel for onsite execution.
The MDL transpooling spread consisted of MDL Second-generation Reel Drive System for handling the installation reels, 150Te reel drive system for handling the transportation reels, two 2-track pipelay tensioners to ensure controlled constant tension to protect the product, a pipe straightener, deck deflectors, roller assemblies and winches.
The spread was supplemented by Client-contracted welding, NDT and field joint coating equipment and services, which allowed MDL to optimise the equipment layout to provide tie-in weld services. The equipment spread provided fail safe control during the onshore spooling campaign, with MDL tensioners also providing control for tie-in weld in the firing line.
Prior to the operation in Norway, straightening trials were carried out in MDL‘s facility in Scotland using the transpooling tensioners, pipe straightener and a product sample.
Steven Morrison, MDL Project Engineering Manager, said: “This has been a great project for MDL, as we offered and executed a true value-adding package for two clients during a single mission, against the backdrop of the ongoing pandemic and the associated travel and personnel restrictions.
“Our pipelay equipment – the base case for carrying out the transpooling – is already well known for improving efficiency of SURF operations, while our supervisors and technicians are recognised for their professionalism and expert knowledge. In this case we called on our experiences with the handling of coiled tubing product and were able to implement risk-reducing measures in our pre-engineering to optimise the onsite execution.
“This campaign also reiterates our in-house design and engineering capabilities, where we offer a whole new level of savings to our clients, by streamlining the engineering, management and execution of their projects.
“This was also a great example of collaboration for cost efficiencies in a challenging market. Even though the products were destined for two different fields, our clients worked together to deliver a single transpooling campaign.
“Effectively that meant a 100% cost saving on project engineering, mobilisation costs, equipment rental and personnel rates, compared to carrying out two separate transpooling campaigns – adding true value to the end client.”