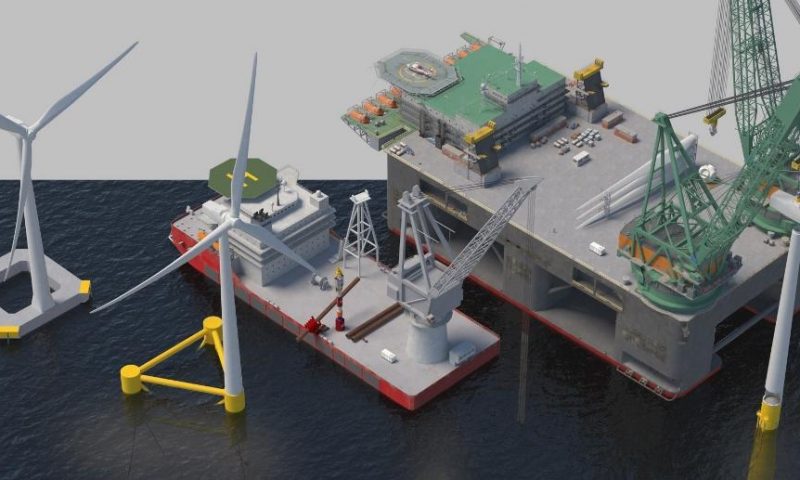
IHC IQIP Explores and Invests in Floating Wind Technologies
With up to 80 percent of the world’s potential offshore wind resources located at depths beyond the limit of the monopile, attention is turning to the prospect of floating foundations. IHC IQIP, a market leader in the supply of piling spreads for moorings, has already put its expertise to use in the construction of the world’s first floating wind farm.
With a new report from DNV GL predicting that the capacity of floating wind will make up more than 20% of the offshore wind market by 2050, the potential of floating wind is everything but up in the air. In fact, the advantages are obvious: Without the water depth constrictions of monopiles and jackets, floating substructures will be able to reach areas of stronger wind allowing turbines to yield a greater energy output; they will remove environmental concerns from shorelines, and, as some structures can be assembled in ports and tugged out to sea by smaller vessels, floating wind offers the potential of local supply chains.
However, so far, the technology has only been applied in small-scale projects, and, when it comes to the development of larger wind farms, industrialised manufacturing and efficient installation will be of essence to make floating wind as profitable as bottom fixed wind.
“What we have seen so far are single floating units, like with oil and gas platforms, moored to the seabed with multiple mooring lines and anchors, but it’ll be interesting to see what methods will be used in larger-scale projects,” says IHC IQIP Business Developer Niels de Vos, who wrote his thesis on floating wind.
However, De Vos strongly agrees that floating wind will open up new opportunities, especially he says, for regions where shallow waters are scarce, like California and Norway, but also for countries where the most attractive sites closer to shore are already allocated.
Exploring a new market with known techniques
Put into operation in 2017, Hywind Scotland became the world’s first floating wind farm. The installation of its five six-megawatt turbines on spar-buoys was completed with the help of IHC IQIP’s Flange Clamp Tool. The tool helps solve a potentially costly challenge in the installation of floating wind, namely that Spar type floaters, due to their large draft, typically require offshore assembly. Allowing for a temporary axial connection between the floating substructure and the tower, the Flange Clamp Tool can save time and resources in this process.
“Without any personnel needed inside the turbine during assembly, and permanent bolting done outside costly vessel time, IHC IQIP improved both the safety and efficiency of the installation at Hywind Scotland,” stresses de Vos adding: “However, IQIP’s turbine installation tools can also ensure safe and efficient port-side assembly.”
Another challenge arising with floating wind farms is the efficient installation of mooring lines. A tool that can ease the process is IQIP’s Subsea Connection Frame which allows mooring lines to be pre-laid on the seabed prior to the arrival of the wind turbine.
“Our Subsea Connection Frame is used to connect mooring lines underwater with a standard H-link. Perhaps this may even allow mooring lines to be post-laid as lines could be connected to the floater in the port and then released at the wind farm site for subsea connection. Once connected, IQIP’s Subsea Tension Tool can provide rapid underwater tensioning of new or operational mooring lines which eliminates the need for tensioning equipment on each floating wind turbine.” explains de Vos.
Floating new ideas
An essential component of the mooring system is reliable anchors, which can be accurately installed with driven piles using IQIP’s piling spread. The complete spread includes pile handling and lifting equipment which places the pile securely into a subsea pile guiding frame. Placed on the seabed, the frame supports, levels, and orientates the pile, ensuring that the mooring line connection is pointed towards the wind turbine before the Hydrohammer smoothly installs it into the seabed.
The advantages of this technology will become even more evident, predicts de Vos, as floating wind farms increase in size, making mooring solutions and floater designs specifically tailored to reduce installation time, costs, and associated risks essential.
“I think that the fact that driven piles can withstand both vertical and horizontal loads from the floating wind turbine, even from multiple directions, will make them part of the solution. It means less piles could be strategically positioned in the wind farm to keep multiple floating wind turbines stationed, allowing for a cost-reducing shared mooring system.”
Overall, the emerging floating wind market still has an ocean of open opportunities to be explored.
“But no matter which solutions we’ll see,” says de Vos, “IQIP is ready to participate.”