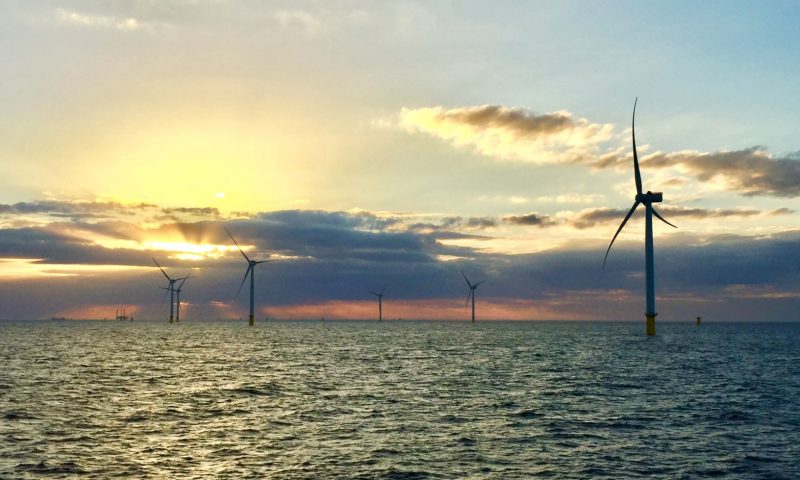
Siemens to Supply High-Voltage Equipment for Major U.S. OWF Project
Siemens has been awarded an order from Danish customer Semco Maritime to provide the main electrical equipment for the electrical service platform (ESP) of the offshore wind project Mayflower Wind LLC (Mayflower Wind). The project is located in a federal lease area approximately 25 miles south of Nantucket, Massachusetts in the United States, and will have a capacity to generate up to 1.6 gigawatts (GW) of renewable energy. Siemens will supply the components for Semco Maritime by 2022.
Earlier this year, a joint venture between the Danish companies Bladt Industries and Semco Maritime was chosen by end customer Mayflower Wind – a joint venture of Shell & EDP Renewables – to design and construct the electrical service platform of the offshore project Mayflower. Semco Maritime has now awarded Siemens with the contract for the delivery of the high-voltage electrical equipment for the ESP, including three 275 kV / 265 MVAr shunt reactors, a 72 kV HV gas insulated switchgear (GIS), three 275 kV MV GIS systems, integrated conditioning monitoring system and SCADA and protection systems.
“At Semco Maritime, we have for a number of years created a very strong track record to deliver competitive quality projects in electrical infrastructure for offshore wind. We are looking forward to the cooperation with Siemens, who is a competent and reliable partner,” says Carsten Nielsen, Senior Vice President of Renewable Energy at Semco Maritime.
“We are proud of the opportunity to bring our expertise in offshore transmission to Mayflower Wind, a project that will lead the way for increasing the share of clean, renewable energy in the U.S. energy mix. The offshore Center of Competence in Denmark did an outstanding job in creating a comprehensive, tailor-made solution for this exciting new project, making the best use of our broad transmission portfolio”, says Beatrix Natter, CEO of the Transmission division at Siemens Energy.
The system solution is specifically designed to significantly reduce both the size and weight of the platform, lowering the need for the use of steel in the construction and thus making the platform more resource- and cost-effective.